DESCRIPTION AND OPRATION
Batteries are widely used to provide direct-current electrical energy to the aircraft and are normally used as a secondary or standby power source. In a battery, a number of cells are assembled in a common container and connected together to function as a source of electrical power.
There are two types of aircraft batteries in common use today: lead-acid and nickel-cadmium. Both of these devices use positive and negative plates in an electrolyte.
Figure below shows how aircraft batteries look like (nickel-cadmium type).
1. LEAD-ACID BATTERIES:
The lead in the grid of the negative plate and the lead peroxide in the positive plate change when a connection is made across the terminals of the battery. The electrolyte enters into this change, not only as a conductor, but as an active participant.
Lead-acid batteries used in aircraft are similar to automobile batteries. The cells of a battery are connected in series. Each cell contains positive plates of lead peroxide, negative plates of spongy lead, and electrolyte (sulfuric acid and water).
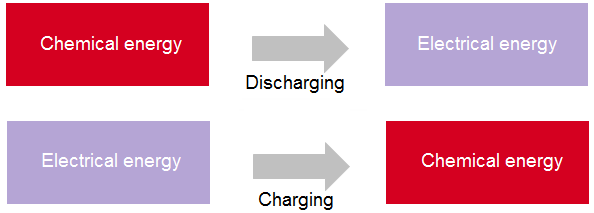
In discharging, the chemical energy stored in the battery is changed to electrical energy; in charging, the electrical energy supplied to the battery is changed to chemical energy and stored. It is possible to charge a storage battery many times before it deteriorates permanently.
1.1. Lead-acid cell construction:
Each plate consists of a framework called a grid, made of lead and antimony, to which the active material (spongy lead or lead peroxide) is attached. The positive and negative plates are so assembled that each positive plate is between two negative plates. Thus, the end plate in each cell is a negative plate.
Between the plates are porous separators which keep the positive and negative plates from touching each other and shorting out the cell. The separators have vertical ribs on the side facing the positive plate.
This construction permits the electrolyte to circulate freely around the plates. In addition, it provides a path for sediment to settle to the bottom of the cell.
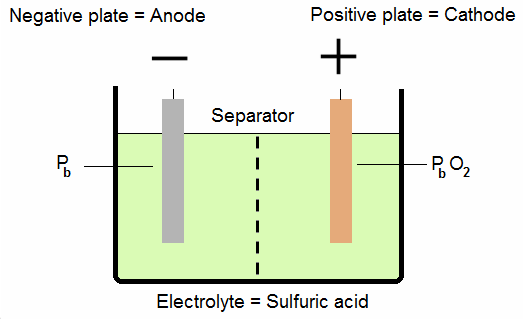
Grid:
A grid cast of an alloy of lead and antimony forms the framework for the active elements in the lead-acid battery. The antimony in the lead makes possible finer castings so there will be room for more active material.
Negative plates:
The grids which serve as the negative plates have their openings filled with a dull grey, spongy mass of porous lead. This lead has a material, called an expander, mixed into it to keep it from contracting back into its dense form and losing the surface area needed for battery capacity.
Positive plates:
The grid of the positive plate is filled with a compound of lead peroxide. This is a highly porous, chocolate brown crystalline substance.
Separators:
Negative and positive plates are assembled into cell elements.
Between each pair of plates is a separator usually made of microporous rubber material, having vertical ribs next to the positive plate. This ribbing allows a greater volume of acid to be held in contact with the positive plates and improves the efficiency of the cell.
A loose fiberglass mat is sometimes placed next to the positive plate to retard the loss of the lead peroxide after continued cycling.
Cell elements:
In the cell elements there will always be one more negative plate than positive, so the negative will be able to protect the more active positive plate, and prevent warpage by exposing both sides equally.
A connector strap is welded onto each plate. The number of plates in an element has no influence on cell voltage, but the area relates to the ampere-hour capacity of the battery.
Containers:
A high impact, melded case houses the cell elements to make up the complete battery. These cases have compartments for each cell. The bottom of the compartment is ribbed with four element rests, two of which support the negative plates, and two which support the positive.
This alternate support minimizes the possibility of internal shorting of the cell. A space exists below the plates in which any active material lost from them can accumulate without causing an internal short.
Battery venting:
Battery fumes and gases may cause an explosive mixture or contaminated compartments and should be dispersed by adequate ventilation.
Venting systems often use ram pressure to flush fresh air through the battery case or enclosure to a safe overboard discharge point.
The venting system pressure differential should always be positive, and remain between recommended minimum and maximum values. Line runs should not permit battery overflow fluids or condensation to be trapped and prevent free airflow.
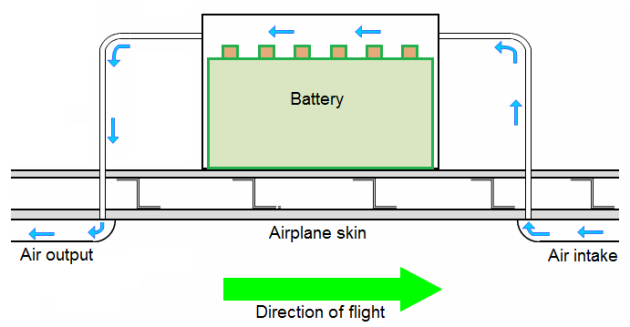
Venting systems often use RAM pressure to flush fresh air through the battery case or enclosure to a safe overboard discharges point. The venting system pressure differential should always be positive, and remain between recommended minimum and maximum values.
Line runs should not permit battery overflow fluids or condensation to be trapped and prevent free airflow.
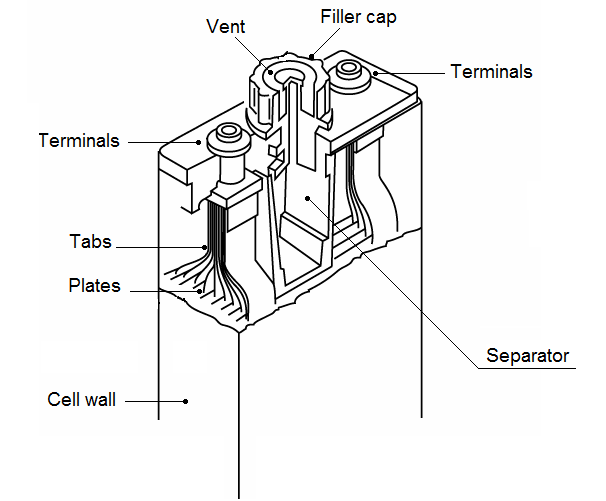
Battery sump jars:
A battery sump jar installation may be incorporated in the venting system to dispose of battery electrolyte overflow. The sump jar should be of adequate design and the proper neutralizing agent used.
The sump jar must be located only on the discharge side of the battery venting system.
Battery boxes are vented to the outside of the airplane by air forced through swoops. The exit vent incorporates a neutralizing solution in a sump jar.
There are two basic types of containers for aircraft batteries: vented and unvented. Vented batteries are mounted in the airplane without a separate box. There are some systems of vents; the most used are the “NACA” type or the “blower” type.
Batteries without vent provisions must be installed in a suitably vented box.
1.2. Lead-acid cell discharging:
The lead in the grid of the negative plate and the lead peroxide in the positive plate change when a connection is made across the terminals of the battery. The electrolyte enters into this change, not only as a conductor, but as an active participant.
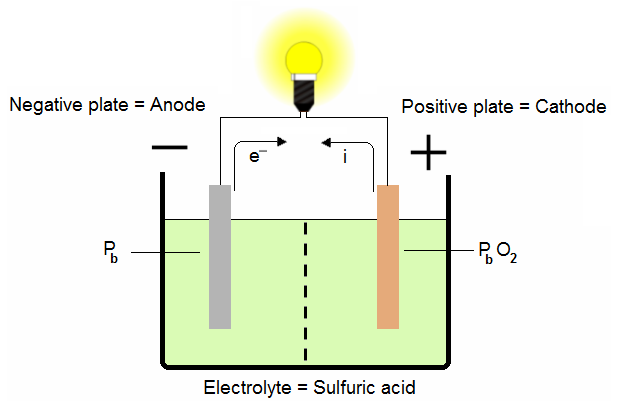
At the anode the sponge lead gives lead sulfate:
Electrons are created and circulate from the anode to the cathode through the resistance.
At the cathode the lead dioxide gives lead sulfate:
1.3. Lead-acid cell charging:
When the active elements of both plates become lead sulfate, and the electrolyte is diluted, there is no more chemical energy to change to electrical energy. The battery is said to be discharged.
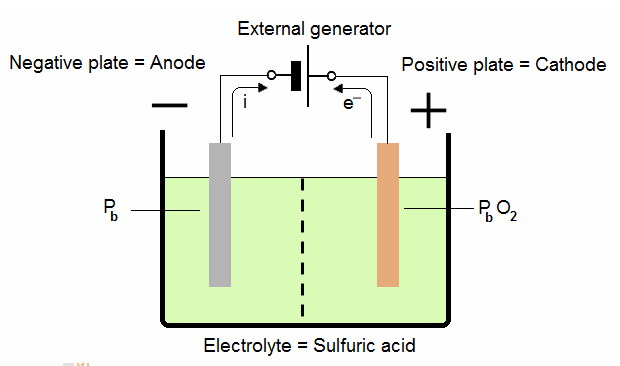
The battery can be returned to a condition of charge by reversing the current flow. We use a external direct current generator to charge the battery.
At the anode the lead sulfate gives sponge lead sulfate:
A generator or other source of direct current is attached to the battery with its positive terminal to the positive plate. Electrons are forced into the battery at the negative terminal.
This drives the sulfate radicals from both the positive and negative plates back into the electrolyte where they change the water back into sulfuric acid.
At the cathode the lead sulfate gives lead dioxide:
If a battery is allowed to sit for a period of time in a discharged condition, or if the electrolyte level is low for some time, the lead sulfate will harden and be difficult to convert back to lead and lead peroxide. A battery in this condition is said to be sulfated.
Conditions of charge:
The electrolyte changes its density, the relative amounts of acid and water, as the condition of charge changes. It is possible, therefore, by knowing how much acid is in the electrolyte to know the condition of charge of the battery. An instrument known as a hydrometer is used to determine this condition.
A small weighted float with a long stem and a numbered scale is held in the enlarged tube of a syringe. Electrolyte is pulled up in this tube where its density is indicated by the level the float rides in the liquid.
The number opposite the level of electrolyte is its specific gravity. Specific gravity is the ratio of the density of the electrolyte to the density of pure water.
The electrolyte used in lead-acid aircraft batteries is concentrated sulfuric acid (H2S04), having a specific gravity of 1.835, diluted with pure water to a specific gravity of 1.265 to 1.275 at 80 degrees F.
When the specific gravity of the electrolyte has been reduced by discharging to about 1.150, there is not enough chemical strength to further change the lead into lead sulfate, and the battery is said to be discharged.
We can use a hydrometer to test Specific Gravity and State of Charge in batteries with removable caps.
Here's how:
Remove the battery caps. Check the electrolyte level. Make sure all cells are covered but not overfilled.
Insert the hydrometer into each cell and draw electrolyte into the glass cylinder with the squeeze ball. Draw just enough acid into the cylinder to make the float rise.
Hold the hydrometer vertical as each sample is drawn. Note the exact level at which the fluid level intersects the measurement scale on the float and record it.
Repeat the test at each of the remaining cells. Record the reading for each cell. Compare readings to the chart on this page to determine state of charge.
If the battery is below 75 percent state of charge, recharge it before load testing.
Charging the battery will cause the sulfate radical to leave the plates and combine with the water to reform sulfuric acid. When the battery is fully charged the specific gravity will be about 1.275.
Temperature affects the density of a liquid, so a temperature correction must be applied to the electrolyte specific gravity before it is completely meaningful. When the electrolyte is cold, it is more dense than standard, and this increased density could be erroneously interpreted to be caused by the condition of charge.
Conversely, electrolyte temperature above standard would cause the liquid to be less dense and could indicate a state of charge below its true condition. For this reason, it is extremely important when talking a reading of specific gravity to know the temperature of the electrolyte.
Some of the better hydrometers have a thermometer built into the instrument. With others, the temperature must be taken with a separate thermometer and a correction applied Figure shows the correction to apply.
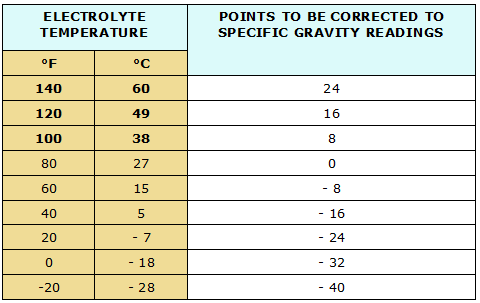
As you see it is 0.004 point for every ten degrees Fahrenheit (°F) that the temperature varies from the standard of 80 °F. For example, an electrolyte having a specific gravity of 1.240 at 100 °F would have a corrected specific gravity of 1.248.
We find this by the fact that the electrolyte is twenty degrees warmer than the standard of 80 °F, and is therefore less dense by 0.008 gravity points; 1.240 plus 0.008 equals 1.248.
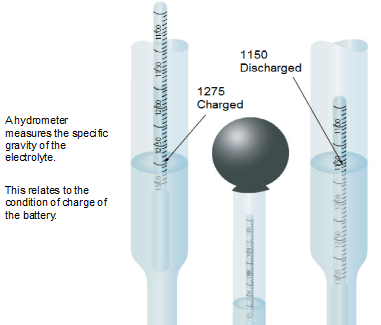
1.4. Lead-acid cell rating:
Voltage:
The voltage of a lead-acid aircraft battery is determined by the number of cells. For instance, a battery having six cells and an electrolyte with will have an open circuit voltage of 2.00 volts per cell or 12.0 volts.
1.5. Lead-acid battery testing and charging:
Batteries shipped from the manufacturer in a wet charged condition must be maintained in a state of charge. Care must be taken to see that they are not allowed to discharge, or to get low on electrolyte. This places an inconvenience on the supplier and presents problems in warehousing. To make battery storage and shipping less difficult, almost all new aircraft batteries sold today are in a dry charged state.
When the battery is manufactured, the plates are fully charged or formed. They are then thoroughly dried and the battery is assembled. The complete battery is sealed to prevent the entry of air or moisture, and is kept in this condition until placed in service.
A discharged battery may be put back into a charged condition by passing electrical current through it in a direction opposite to that of the discharge.
1.6. Lead-acid battery Installation and servicing:
Anything done to the airplane by an B1.1 technician must be done according to approved data. Servicing batteries is especially true in this regard. Replacement batteries must be of an approved type, and all servicing must be done according to good practices and techniques.
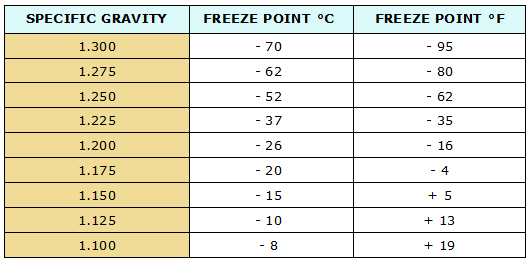
When installing or removing a battery, take special care that an electrical spark is not caused by the wrench shorting the battery out to the structure. To prevent this, always remove the ground cable first, and install it last.
A lead-acid battery is not likely to freeze if it is maintained in a good state of charge. Never add water to a battery if it is going to be subjected to freezing temperatures before it has a chance to be mixed with all of the electrolyte by charging. Table here gives the freezing point of electrolyte with various specific gravities.
2. NICKEL-CADMIUM BATTERIES:
A nickel-cadmium cell, also called NiCa or NiCad cell), contains:
a nickel oxide-hydroxide at the positive electrode plate (solid state),
a cadmium at the negative electrode plate,
a separator and
an alkaline electrolyte (potassium hydroxide).
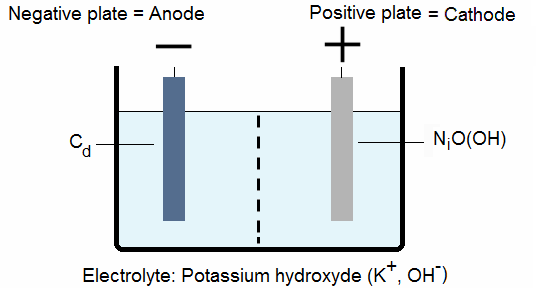
At the cathode the nickel oxide hydroxide gives nickel hydroxide:
At the anode the cadmium gives cadmium hydroxide:
Electrons are created and circulate from the anode to the cathode through the resistance.
2.1. NiCad cell discharging:
The cadmium in the grid of the negative plate and the nickel oxide-hydroxide in the positive plate change when a connection is made across the terminals of the battery. The electrolyte enters into this change, not only as a conductor, but as an active participant.
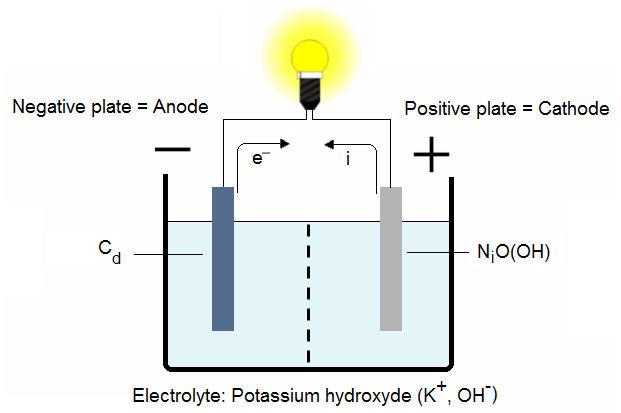
2.2. NiCad cell charging:
When a load is connected across the battery, electrons leave the negative plate and enter the positive, and oxygen is driven from the positive plate to be recovered by the negative.
During discharge, the electrolyte is absorbed by the plates, and the level drops in the cell.
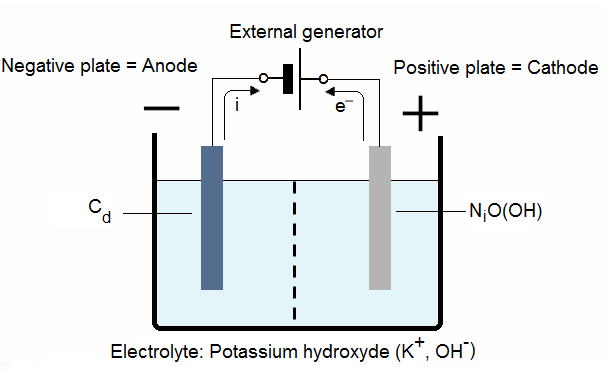
At the cathode the nickel hydroxide gives nickel oxide-hydroxide:
At the anode the cadmium oxide gives cadmium:
Forced electrons are created by the charger and circulate from the cathode to the anode.
One of the characteristics of a nickel-cadmium battery is its constant voltage up to almost the point of complete discharge; another is the fact that the electrolyte does not enter into the chemical changes which cause the charge.
Because of these two facts, there is no simple way to determine the condition of charge of the battery.
The only way to know exactly how much charge it has is to know how many ampere-hours of charge have been put in.
2.3. Thermal problem:
The property of being able to discharge at a high rate and to accept a charge at an equally high rate gives the nickel-cadmium battery a characteristic which is equally undesirable.
The nickel-cadmium battery has a very low internal resistance, and its voltage and this resistance vary as an inverse function of temperature, which means an increase in cell temperature will cause a decrease in voltage and internal resistance.
The temperature rise that triggers thermal problems can come from heat generated by a fast discharge, from high ambient temperatures in a poorly vented installation, or from a breakdown of the separator material.
If the cellophane becomes perforated oxygen can migrate from the positive plate to the negative. It will there unite with the cadmium to generate enough heat to decrease the internal resistance to a dangerous point.
Batteries installed in most airplanes are subjected to a constant voltage charging source, the generator. These generators have a high current producing capability.
Turbine starters require a lot of electrical energy. The battery provides this, and it usually does it without much strain. If the start has been difficult, a high current has been taken from the battery for a prolonged period of time.
The battery, especially the center cells, gets warm. These cells, being warmer than the other cells, have a lower voltage and a lower internal resistance. When the engine starts and the generator gets on the line, a high current is put back into the battery.
Normally as this current is put back into the battery it will drop off rapidly as the battery regains its charge, but if some of the cells are unbalanced because of temperature the current continues to rise causing more heat.
This rise in temperature causes a further rise in current and a condition develops in which the battery accepts all of the charging current the source is capable of producing. This condition is known as a thermal run-away, and can cause so much heat that the battery may explode.
This problem causes operators to look on nickel-cadmium batteries with mixed emotions.
2.4. Battery servicing:
Inspection in the airplane:
Unlike the lead-acid battery, which is usually forgotten except for an occasional check for corrosion and electrolyte level, a nickel-cadmium battery should be carefully monitored for its condition.
Cell shorted for complete discharge in deep-cycle servicing :
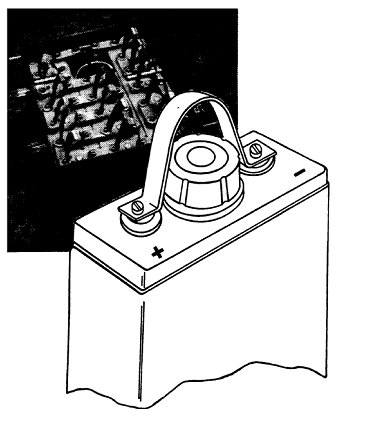
The battery container should be free of any contamination.
The ventilation system should be clear and operating. The pad in the sump jar should be saturated with a boric acid solution. At least every fifty hours, if everything is going right and more often if trouble has been reported, the battery should be inspected for indication of spewed electrolyte, as indicated by a white powder on the top of the battery.
Shop inspection:
Every aircraft manufacturer using nickel-cadmium batteries has a recommended service time for the battery. This is based on hours of flight time or number of engine-start cycles.
The frequency of this out-of-the-airplane inspection is based on the severity of load placed on the battery. Airplanes having parallel starting circuits place a far lighter load on the batteries than airplanes using series starting circuits.
A typical service sequence consists of:
Washing the battery: check the vent caps to prevent water entering the cells, and flush the top of the battery with tap water. Remove any deposits by scrubbing with a nylon or other non-metallic bristle brush. Air dries the battery thoroughly.
Check for leakage current: any conduction between the cell terminal and the case of the battery can cause the battery to self discharge.
Rather than checking for voltage between the case and the cells, it is better to check for current flow existing between these two points.
A voltage could exist and yet cause no excessive current. Set the range of a good multi-meter to the highest current scale (usually around 500 milliamperes). Place the positive lead on the positive terminal of the battery and the negative lead on the battery case, and check for current.
Decrease the ranges until an indication of current is found. Any leakage of more than 100 milliamperes is excessive and the battery should be disassembled and cleaned.
Charge the battery: use a constant current charger or special battery charger/analyzer, and charge the battery at its five hour rate until it reaches the voltage recommended by the manufacturer.
For a typical 19 cell battery, this would be 30 volts, or 1.58 volts per cell. If a constant voltage charger is used, it must be adjusted to the value recommended by the manufacturer, which is now about 1.5 volts per cell. A battery is considered to be fully charged by a constant voltage charger when the charging current tapers off and stabilizes.
Adjust the electrolyte: when the battery is fully charged, its electrolyte will be at its highest in the cells. Measure the electrolyte at this time. It should be at the level recommended by the manufacturer, which is somewhere around ¼'' above the top of the plates. If this measurement is not taken immediately after the charge is terminated, the level will drop and the proper level will be somewhat lower.
Adjust the electrolyte level as required, using only distilled water. No potassium hydroxide should be added, as only water is lost in the electrolysis which occurs when the battery is fully charged.
Discharge the battery: the only way to accurately determine the true state of charge of a nickel-cadmium battery is to discharge it and measure its ampere-hour capacity.
Connect the battery across a load bank and discharge it at the one or two hour rate until an average voltage is reached of 1.0 volt per cell. Note the time. If this discharge time is less than 70% of the time specified by the manufacturer for this particular rate, there is an indication that the capacity of the battery has decreased and a further discharge or equalization is required.
Deep cycling: a battery can lose some of its capacity if one or more of the cells is out of balance with the others.
To remedy this situation the battery must be completely discharged, allowed to remain in this condition for a given period of time, and then charged back to 140% of its ampere hour capacity with a constant current charge.
This is called equalization of deep cycling. Continue to discharge the battery at a lower rate than before, until the individual cell voltage is down somewhere around 0.2 volts.
When this voltage is reached, the cell is considered to be completely discharged. Each cell is then individually short circuited with a shorting strap. The cells should be shorted while the load is applied to prevent sparking at the cell posts.
It may be necessary to short the last few cells in the battery with one ohm, two watt resistors to prevent arcing when the short is applied.
Allow the battery to sit for three to eight hours in this shorted condition to allow all of the cells to reach a completely discharged condition.
Recharging: after the rest period, the battery is placed on a constant current charge at its five hour rate, for seven hours. This will put 140% of its rated ampere-hour capacity into the battery.
In the last five minutes of charge, the voltage of each individual cell is measured. Any cell not having a voltage somewhere between 1.55 and 1.80 volts at a temperature between 70 °F an 80 °F is considered faulty and must be replaced.
Final check: before the battery is returned to service, a final check is made of the torque of all the intercell connection hardware, the level of the electrolyte, and leakage current between the cells and the case.
Any time a battery Is serviced, a complete record should be made of the battery condition. This record will enable you to spot troubles before they become serious.
The record should contain such items as: condition of the case and the individual cells, tightness and condition of the intercell connectors, the electrolyte level and the amount of water added to each cell, the voltage of each cell at the end of the charge, and mention of hot spots or conditions to note on subsequent inspections.
Overhaul:
If a nickel cadmium battery has been serviced in accordance with the manufacturer's recommendations and still does not pass the capacity test, it may be possible for the battery to be overhauled by the manufacturer.
Overhaul of a nickel-cadmium battery consists of complete discharge and emptying. All of the plates are scrubbed clean and dried with hot air. The battery is completely inspected and reassembled, using new separator material.
It is identified as an overhauled unit and is tested to about 90% of the capacity requirements of a similar new battery. The cost of overhaul is somewhere around one-half the price of a new battery.
Special equipment:
Nickel-cadmium batteries with their possibility of thermal problems require careful monitoring in flight.
The Aviation authorities have issued a requirement for equipment to be installed in aircraft using this type of battery for engine or A.P.U. starting to warn the flight crew of impending problems. These warning devices may be of the temperature, current, or voltage sensing type.
Temperature sensing system: one of the more simple temperature monitoring devices uses a temperature sensor to measure the temperature of a central intercell link.
When the temperature of this link reaches 140 °F, a warning light on the panel illuminates to tell the pilot a problem exists, and that he should take the battery off of the generator line.
If the temperature rises to 160 °F, a second light comes on telling the pilot that he does have a problem and should land as soon as possible. A more complex system gives the pilot a direct readout of the battery temperature and activates a warning light when the intercell temperature reaches 150 °F.
Current sensing system: another warning device works on the principle that a thermal problem cannot exist if the charging current is monitored closely.
Voltage sensing system: a third type of warning device operates on the principle that a dangerous thermal problem cannot exist if all of the cells are balanced voltage-wise.
A continual sampling of the voltage of all of the cells is taken and a warning flashed to the pilot if any cell falls outside of a minimum and a maximum voltage range.
This sampling is done at approximately four second intervals. If more than one cell is out of tolerance, the flashing becomes more rapid. To back up this system a temperature sensor is placed between the central cells of the battery to warn the pilot of an over-temperature condition.
Shop equipment:
Servicing nickel-cadmium batteries requires special attention and some special equipment. Most important of all, it requires separate facilities from lead-acid servicing.
The electrolyte and fumes of the lead-acid batteries are exactly opposite the e electrolyte of the nickel-cadmium batteries, so there must be no mingling of the two.
Tools used for servicing lead-acid batteries are considered contaminated and should not be used with nickel-cadmium batteries.
Chargers for both batteries may be of the constant voltage or the constant current type.
Nickel-cadmium batteries, however, require a more sophisticated machine. Any shop servicing nickel-cadmium batteries should have a charger/analyzer. This special type charger has a built-in timer for controlling the charge and charge cycles, load banks for discharge, and voltage monitors for the entire battery and for individual cells.
The charger/tester also has the capacity of placing a simulated starter load on the battery and monitoring the voltage of each cell during this current drain. Also built into this tester is an shorting circuit whereby each cell may be individually shorted while attached to the tester.
Installation:
The advantage of light weight for its high discharge capability has prompted some aircraft operators to replace the lead-acid battery with the nickel-cadmium battery. Whenever this is done, the battery box and surrounding area should be specially treated to prevent contamination.
The compartment should be thoroughly washed and neutralized with ammonia or bicarbonate of soda, and the entire area painted with e resistant varnish. All traces of acid corrosion must be removed.
The entire vent system, including the pad should be replaced with one saturated with a 3% solution of boric acid and water. The sump jar should be completely cleaned and neutralized or replaced.
The sump physical size and weight difference between the lead-acid and nickel-cadmium battery may require a new battery box attachment, and will require a new weight and balance computation.
When making any alteration of this nature, be sure all of the requirements of the airplane manufacturer are met and the proper alteration records are made.