TYPES OF BEARINGS AND THEIR APPLICATIONS
1. BALL BEARINGS:
A ball bearing is a type of rolling-element bearing which uses balls to maintain the separation between the moving parts of the bearing.
The purpose of a ball bearing is to reduce rotational friction and support radial and axial loads. It achieves this by using at least two races to contain the balls and transmit the loads through the balls. Usually one of the races is held fixed. As one of the bearing races rotates it causes the balls to rotate as well. Because the balls are rolling they have a much lower coefficient of friction than if two flat surfaces were rotating on each other.
Ball bearings tend to have lower load capacity for their size than other kinds of rolling-element bearings due to the smaller contact area between the balls and races. However, they can tolerate some misalignment of the inner and outer races.
Compared to other rolling-element bearings, the ball bearing is the least expensive, primarily because of the low cost of producing the balls used in the bearing. There are several common designs of ball bearing, each offering various trade-offs. They can be made from many different materials, including: stainless steel, chrome steel, and ceramic. A hybrid ball bearing is a bearing with ceramic balls and races of metal.
1.1. Single-row ball bearing:
a) General:
The rigid bearing with a row of balls is a bearing presenting a very good performance/price ratio; it is relatively universal.
b) Aptitudes:
It has a good capacity to support the radial loads and also the axial loads in the two directions. It presents a swivelling and exists in an instrumented version making it possible in particular to determine the rotational speed of the shaft.
c) Uses:
This type of bearing is used in all the fields of mechanical engineering in general (flaps, bearings of jet engines, transmissions of helicopters, on-board equipment...). It is available with a segment which allows an axial immobilization without any retaining wall in the housing.
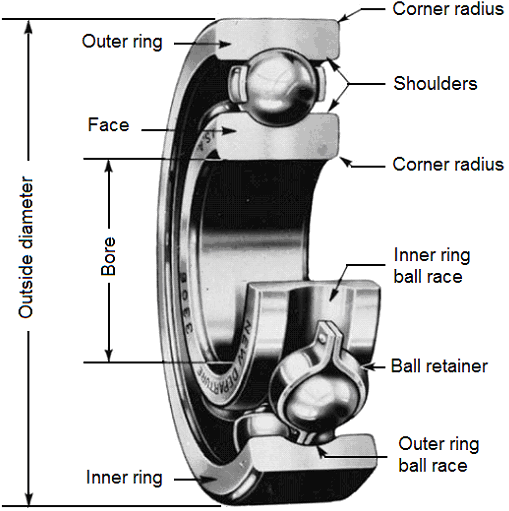
1.2. Double-row ball bearing:
a) General:
These bearings require a good coaxiality between the shaft and the housing.
b) Aptitudes:
This type of bearing allows strong radial and axial loads in the two directions.
A preferential way is sometimes noticed, in case of filling notches. This bearing can be installed alone or together with another bearing (where alignment is necessary).
c) Uses
This type of bearing is used in pumps, reducers (wheel and screw), equipment...
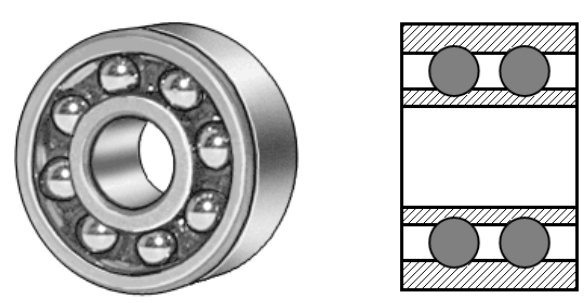
1.3. Double-row self-aligning ball bearing:
a) General:
The self-aligning ball bearing has two rows of balls and a common concave sphered raceway in the outer ring. The bearing is consequently self-aligning and insensitive to angular misalignments of the shaft relative to the housing.
b) Aptitudes:
Self-aligning ball bearings with extended inner ring are designed for less demanding applications using commercial grade shafting. The special bore tolerance allows easy mounting and dismounting.
c) Uses
It is particularly suitable for applications where considerable shaft deflections or misalignment are to be expected.
Additionally, the self-aligning ball bearing has the lowest friction of all rolling bearings, which allows it to run cooler even at high speeds.
S
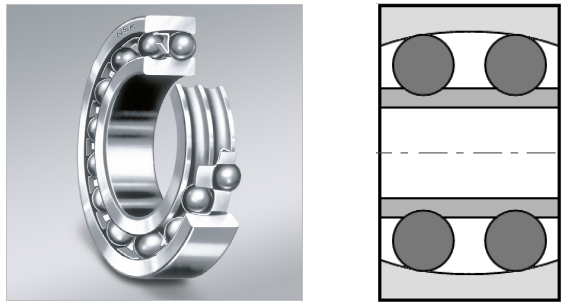
elf-aligning ball bearings with extended inner ring are axially located on the shaft by means of a pin or shouldered screw, which engages in a slot at one side of the inner ring and also prevents the inner ring from turning on the shaft.
When two self-aligning ball bearings with extended inner ring are used to support a shaft, they should be positioned so that the inner ring slots either face each other, or are at the outboard positions of the bearings.
If this is not the case, the shaft is axially located in one direction only.
1.4. Single and double -row angular contact bearing:
a) General:
Angular contact ball bearings have raceways in the inner and outer rings that are displaced with respect to each other in the direction of the bearing axis. This means that they are designed to accommodate combined loads, i.e. simultaneously acting radial and axial loads.
b) Aptitudes:
The axial load carrying capacity of angular contact ball bearings increases with increasing contact angle.
The contact angle is defined as the angle between the line joining the points of contact of the ball and the raceways in the radial plane, along which the load is transmitted from one raceway to another, and a line perpendicular to the bearing axis.
The contact angle varies from 15° to 40° and is measured relative to a line running perpendicular to the bearing axis. Angular contact bearings are unidirectional thrust bearings that can withstand heavy thrust loads and moderate radial loads.
See below: Single angular contact bearing.
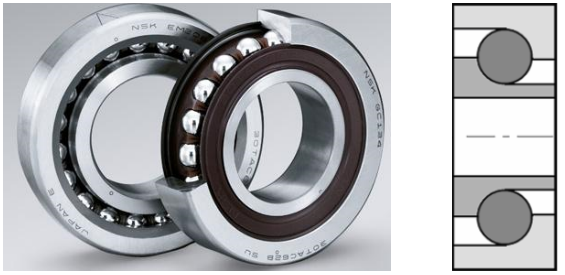
c) Uses:
Angular contact bearings can have a number of different styles of seals or shielding. Seals and shields provide protection from contamination and as a retainer for lubricant.
Seals provide better protection and lubricant containment than shields, but have lower maximum speed capabilities.
Bearings with ball screw support are specially designed for use in ball screw or lead screw applications.
Some bearings may also be flanged. Angular contact bearings may have a variety of lubrication options.
See below: Double-row angular contact bearing.
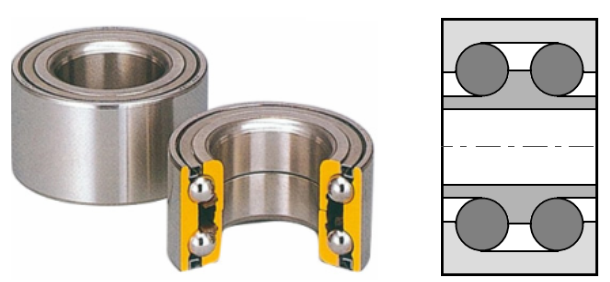
2. ROLLER BEARINGS:
Roller bearings are one of the most widely used industrial bearings. They are called as roller bearings because they are able to carry a load by placing round elements between the two pieces. With the movement of the two pieces, these round elements roll, thereby helping to carry the load.
Most roller bearings use cylinder whose length is slightly greater than its diameter. Roller bearings have higher radial load capacity compared to ball bearings but higher friction and a low axial capacity under axial loads.
2.1. Applications of roller bearings:
Roller bearings are used in rotary applications to replace sliding movement with low friction, rolling.
Automated roller bearing setting techniques offer many advantages like reduced setting time, assembly cost, and and reliable setting. To select the right roller bearing, one must determine the desired bearing life and a sufficient basic dynamic load rating to meet that life requirement.
Roller bearings are used in power generation, wind turbines, gear drives, rolling mills, machine tool spindles, gear reduction units etc.
Roller bearings are the earliest known type of rolling-element-bearing.
2.2. One row, two row cylindrical bearings:
a) General:
This type of bearing supports axial loads only in one direction. They are thus generally used in pairs, opposing each other. Their play must be regulated in order to obtain a good rigidity for the connection. They can also be installed side by side.
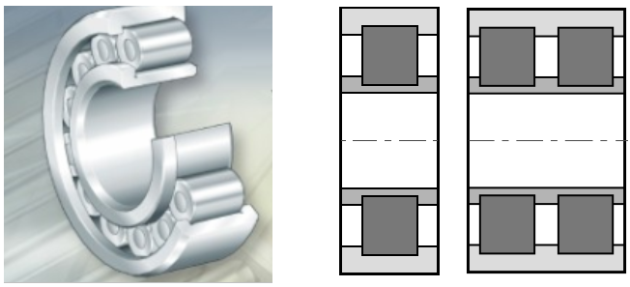
b) Aptitudes:
These bearings support loads combined with predominant axial component at high speeds. The standard bearings have a contact angle of approximately 40°, whereas the precision bearings have angles of 15° or 25°. The bearings installed by pairs have speed limits weaker than the simple bearing.
c) Uses:
These bearings are found in many aircrafts, bearings for jet engines, electric motors, alternators, brushes for machines, etc
2.3. One row cylindrical bearings:
a) General:
This type of bearing is generally used to solve alignment problems due to position defects or deformations. Acceptable range varies from 1.5° to 3°. This type of bearing can sometimes be found on conical sleeves.
b) Aptitudes:
A swiveling is possible due to the spherical shape of the track of the external ring. However, the specific contacts between the balls and the external rings, allow only moderate loads, especially axially.
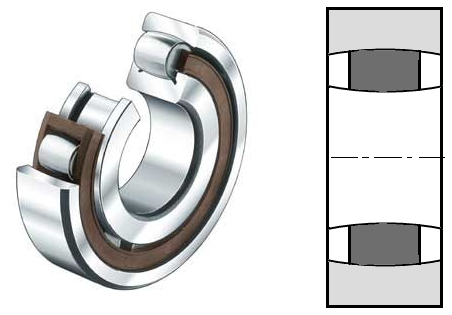
c) Uses:
These bearings are used to prevent a misalignment due to the bending of the shaft or a position defect. They are available with taper bore.
2.4. Two row cylindrical roller bearings:
a) General:
Spherical bearings have a capacity to carry high loads tolerate shocks loads, and are self aligning. As they can tolerate limited speeds, spherical bearings are used in vibrators, shakers, conveyors, speed reducers, transmissions, and other heavy machinery.
Spherical bearings can accommodate a shaft or rod with varying misalignment. They consist of a plain bearing, with a ball bushing, inside a cylindrical housing. The housing may have a liner of different material to minimize friction or provide self-lubrication. Many ball and liner materials are available with different ratings for load capacity and lubrication requirements.
Spherical bearings are relatively maintenance-free. Spherical plain bearings and plain bushes are suitable for applications involving swivel movements, high alternating loads, very high radial loads with a unilateral load direction and high shock loads
Two-row, or double-row, cylindrical bearings are designed for additional strength in carrying radial loads.
These bearing types are interchangeable so the dimensions and diameter under the rollers and diameter over the rollers are held to an ISO/DIN standard. Interchangeability is designed for the ring without the rollers to allow interchange with competitor inner rings.
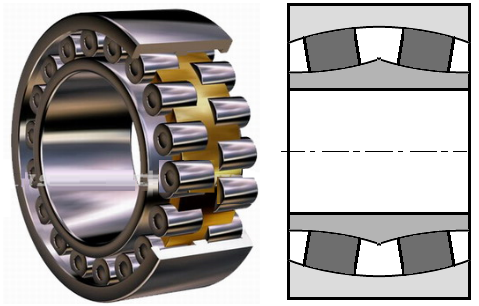
b) Aptitudes:
Due to the linear contact of the rollers on the pathway, these bearings support very high radial loads and rather high speeds. As the rings are separable, the assembly generally does not cause any problem.
c) Uses:
These bearings are used when the radial load is increased: turbo compressors, bevel gear track, but also tachometer generators, bearings, etc.
2.5. Conical tapered roller bearings:
a) General:
These bearings consist of an internal ring (the cone), conical rollers spaced by a cage and an external ring (the basin) separated from the rest. They support the axial loads only in one direction and are generally installed in pairs, opposing each other. Their play must be adjusted.
b) Aptitudes:
They are bearings adapted to the high axial and radial loads, but they do not support high rotational speeds. For high axial loads, a bearing with a significant contact angle, which can vary from 10° to 30°, is used.
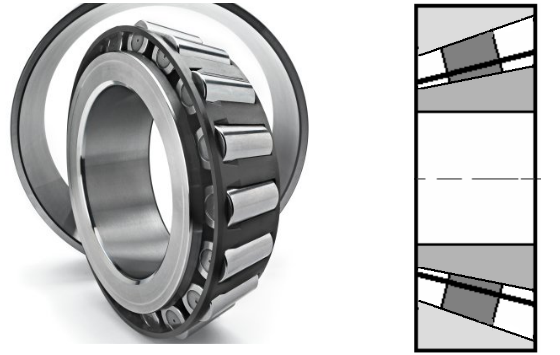
c) Uses:
They are installed in reducers, wheels of the landing gear, etc
2.6. Needle bearings:
a) General:
The use of an internal ring avoids the treatment of the shaft. The main advantage of this bearing is that its overall dimension is reduced.
Needle bearings are widely used industrial bearings, having roller bearings of high length-to diameter ratios
b) Aptitudes:
This type of bearing supports strong radial loads, but not the axial load. Moreover, it requires a good alignment.
The aptitudes of needle bearings depend of the types of these bearings.
Types of needle bearings:
Loose - needle bearings refer to full complement of needles placed within the annular space between two hardened machine components. This structure forms the bearing raceways minus any retainers. Needle bearings are sensitive to misalignment and render a moderate speed capability to the bearing assembly.
Caged assemblies refer to the roller arrangement where the retainer is placed between two hardened machine elements which act as raceways. The have greater speed capacity than loose - needle bearings. The only draw back is that the smaller complement of needles reduces load capacity for the caged assemblies.
Drawn-cup, full-complement needle bearings consist of a deep-drawn cup with a full complement of needles. In some, the needles are retained by the cup lips, in others by the grease.
Drawn-cup, caged needle bearings are identical to full-complement bearings, except that a cage is used. They provide higher speeds and reduced load bearing capacity and have better tolerance for misalignment.
Heavy-duty needle bearings have a heavy outer ring made from materials, load capacity is higher
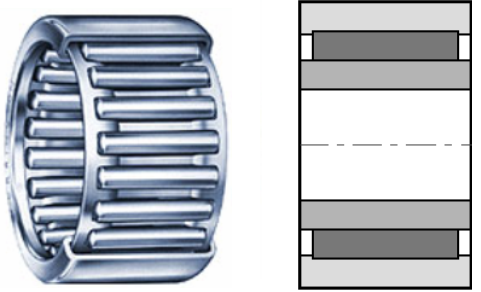
c) Uses:
Needle bearings are widely used industrial bearings, having roller bearings of high length-to diameter ratios. Mostly used in aircraft construction equipment, gear pumps, gasoline engines, and other engine components like rocker arm pivots, compressors, pumps, and transmissions.